Hello Folks,
As some of you know my house (house itself has masonry/concrete exterior walls) has an all season room addition that was and still is in a state of disrepair. About a year ago I repaired some major roof damage and leaks (sheathing, epdm, etc). Recently I also happened to address some rotten and deteriorating 2x4 sole plate and studs issues as shown below:
(removed siding consisting on 3/4 wood from lower corner, and washed it with bleach)
(inside view with sole plate already removed)
(then I rammed and butted the new section of lumber to the existing sole plate)
(other corner with bottom siding mostly installed)
The old siding is made out of mansonite popular during 70s feels like high density cardboard, and in spite of the painting be peeling off it is in solid shape. Currently, I am installing groove and tongue wood boards. In the bottom I added ½ rigid insulation , then wrapped that bottom section with construction housewrapper.
The lower lower portion of the siding is made of ¾ wood (not sure what it is called) and at some point the concrete slab at the bottom gets uneven which made the new wood siding planks uneven with each other thus creating unsightful gaps and misalignment, so I used a compass to transfer the unevenness of the slab to the bottom of the new tongue and groove wood siding plank and then cutted the line with a jigsaw and circular saw.
As some of you know my house (house itself has masonry/concrete exterior walls) has an all season room addition that was and still is in a state of disrepair. About a year ago I repaired some major roof damage and leaks (sheathing, epdm, etc). Recently I also happened to address some rotten and deteriorating 2x4 sole plate and studs issues as shown below:
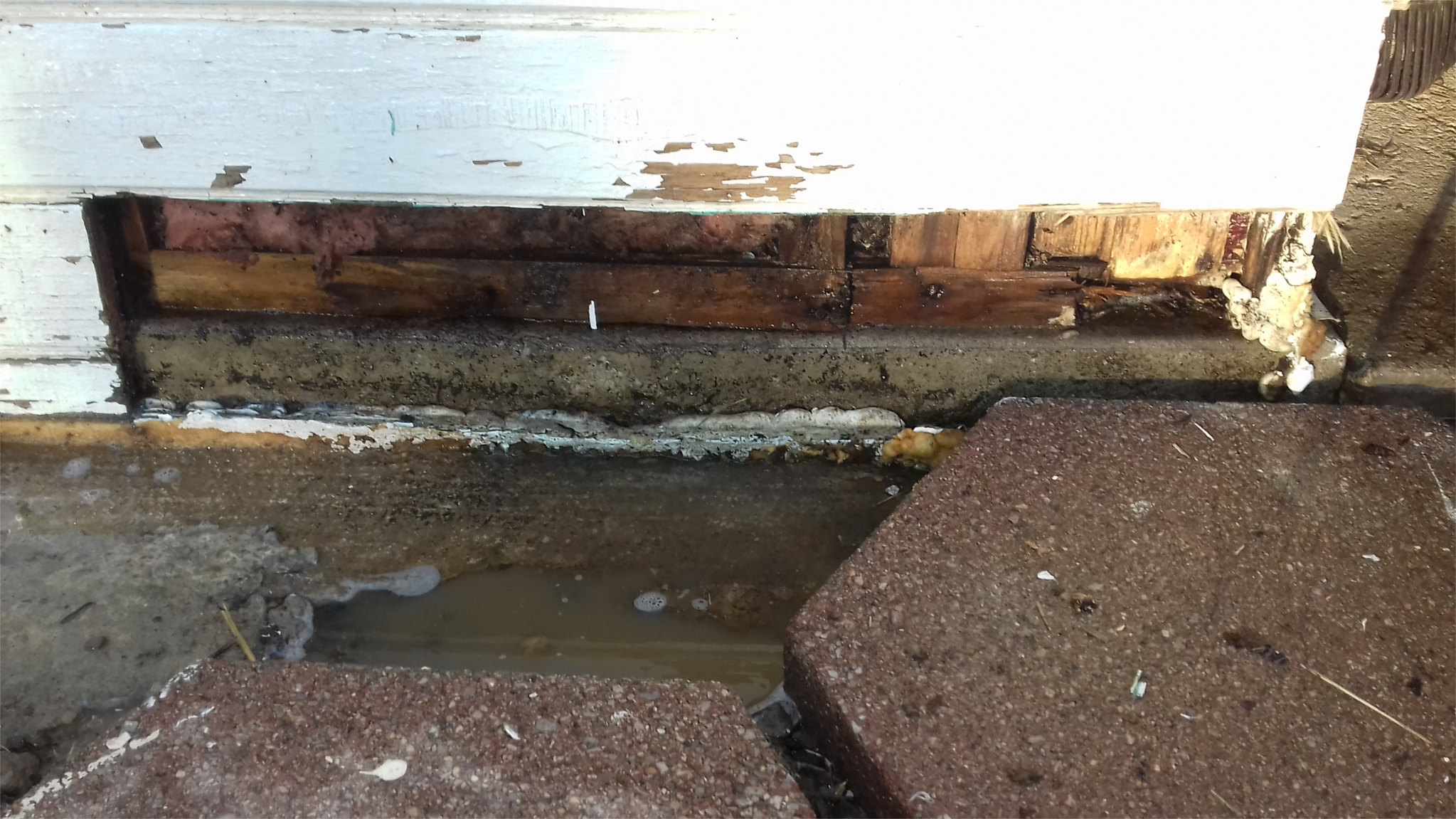
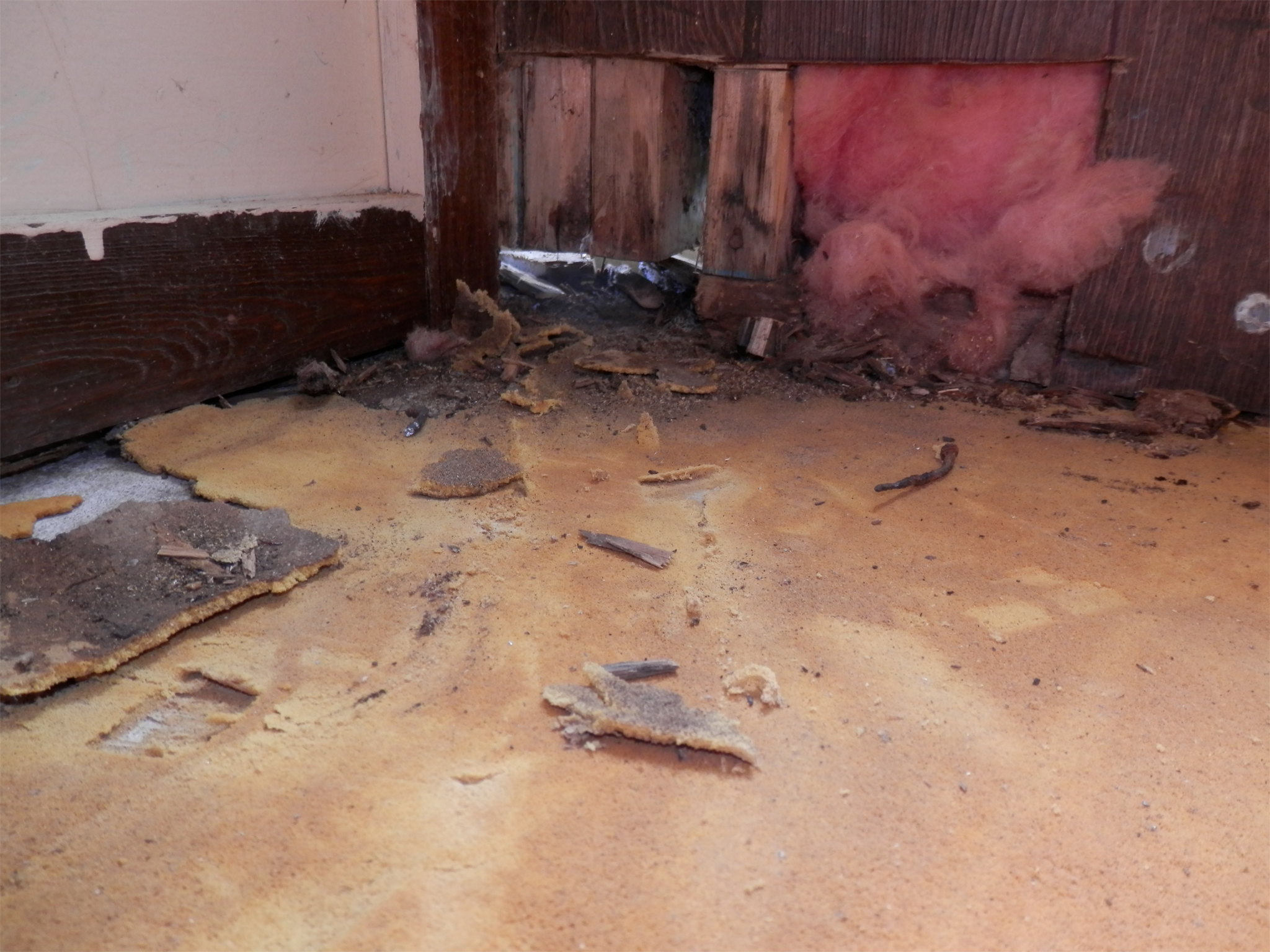
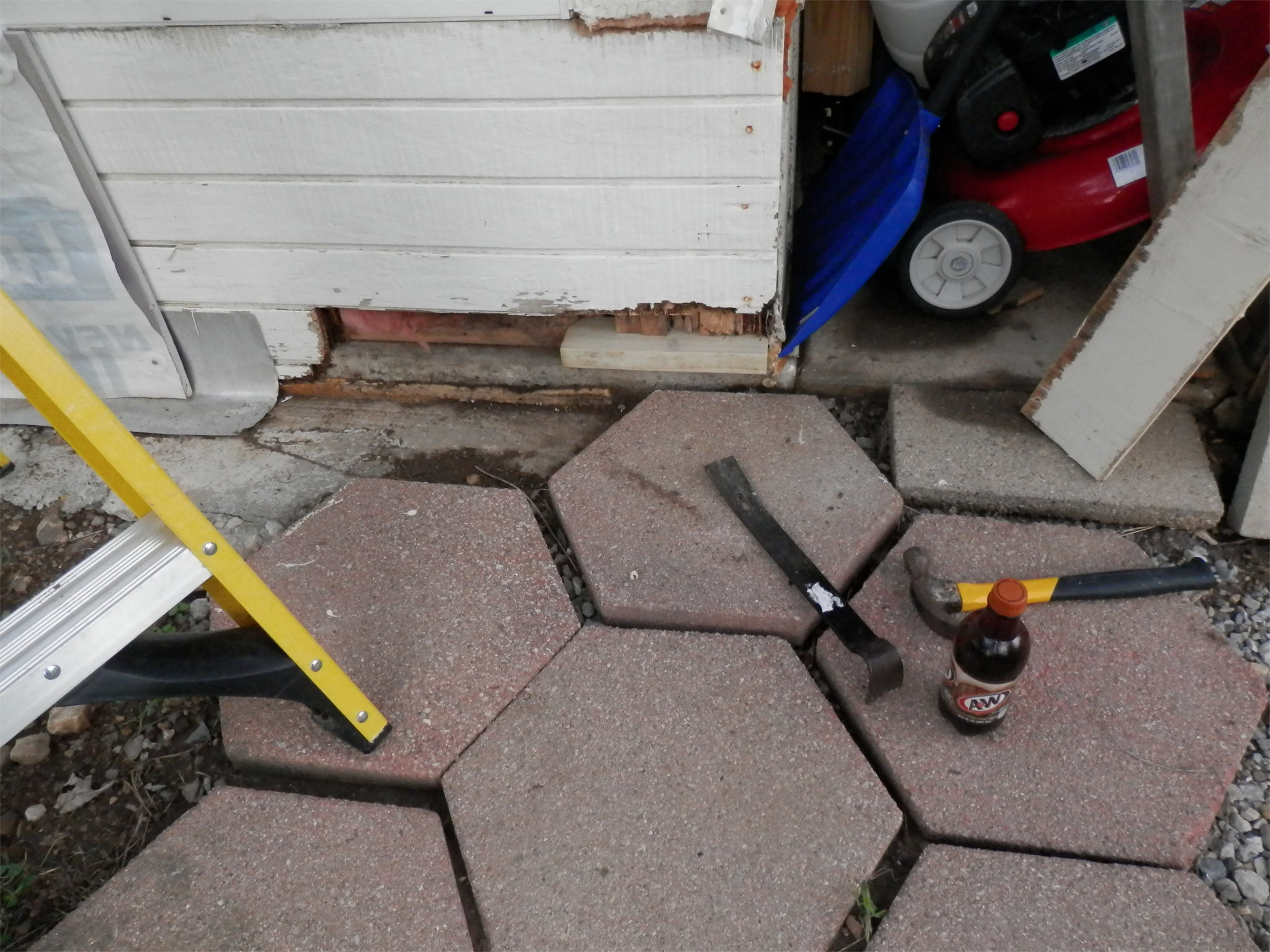
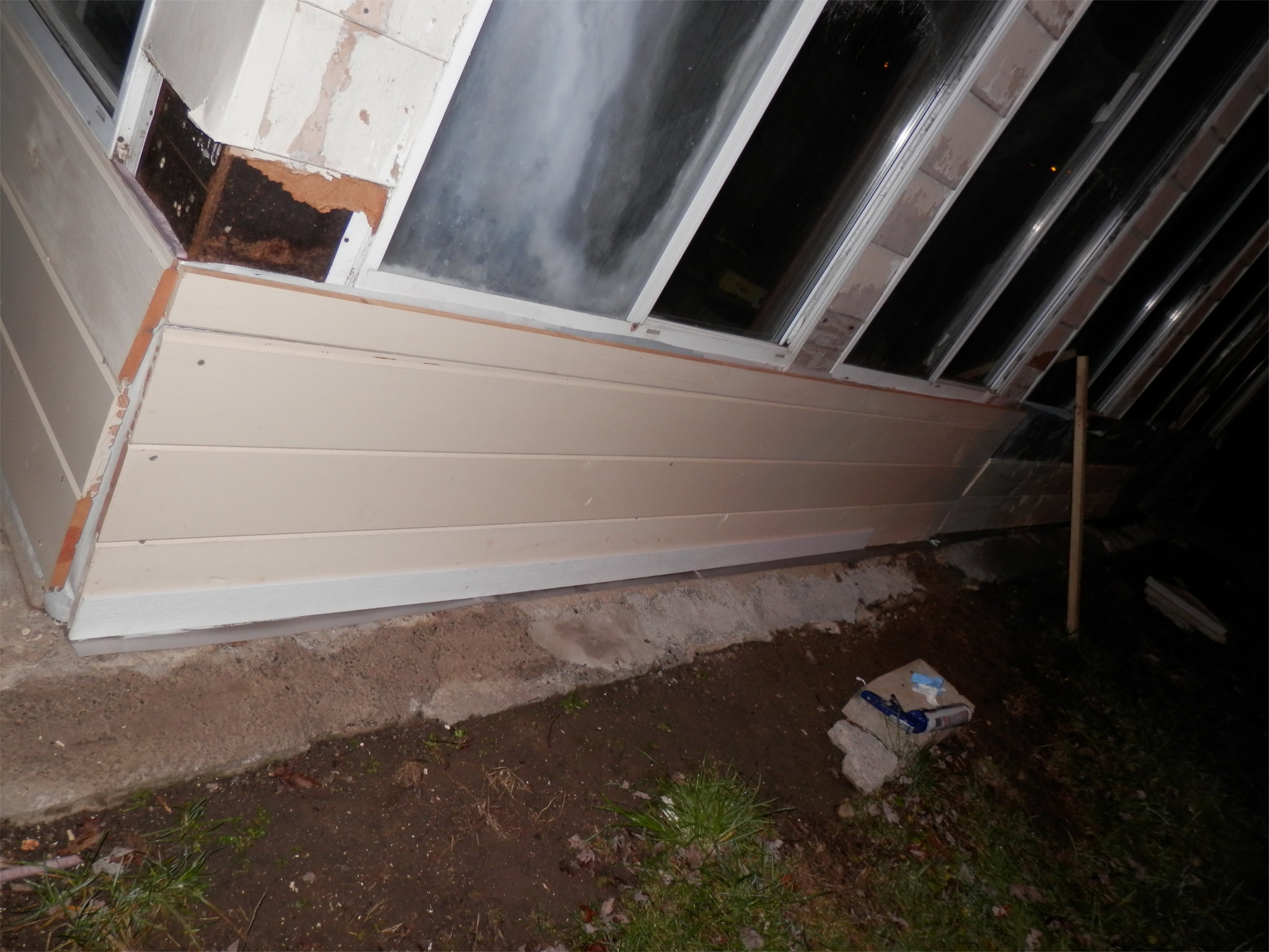
The old siding is made out of mansonite popular during 70s feels like high density cardboard, and in spite of the painting be peeling off it is in solid shape. Currently, I am installing groove and tongue wood boards. In the bottom I added ½ rigid insulation , then wrapped that bottom section with construction housewrapper.
The lower lower portion of the siding is made of ¾ wood (not sure what it is called) and at some point the concrete slab at the bottom gets uneven which made the new wood siding planks uneven with each other thus creating unsightful gaps and misalignment, so I used a compass to transfer the unevenness of the slab to the bottom of the new tongue and groove wood siding plank and then cutted the line with a jigsaw and circular saw.