mustanggarage
Garageaholic
- Joined
- Nov 26, 2009
- Messages
- 903
- Reaction score
- 0
we finished up the short block today. I ran into a bit of a snag though. those used AFR heads I bought turned out to not be in nearly as good a shape as they were supposed to be. so I am going to buy some new ones. I used the old ones to check the piston to valve clearance and to measure the push rods. then we put the front cover on. dang chinese front cover the seal doesn't fit right. I had to grind it off a bit to get it in.
when I put the front cover on I like to put the harmonic balancer on to center the balancer in the front cover seal before I tighten the bolts on the front cover. then since most of the bolts holding the front cover on also go through the water pump I put it on as well. be sure to pull the backing plate off and add sealer on both sides of the gasket and reinstall the backing plate before putting it on the engine.
then we put the new oil pump and pickup on and checked the pickup to pan clearance with clay again before sealing up the one piece oilpan gasket on and buttoning up the bottom end.
I put a new oil filter on it and taped up the low oil sensor hole to reduce the dirt that can get in there. then I put the old heads and new intake on temporarily and wrapped it back up in plastic to await the new heads and pushrods. it will probably be 2-4 weeks before I get the new heads.
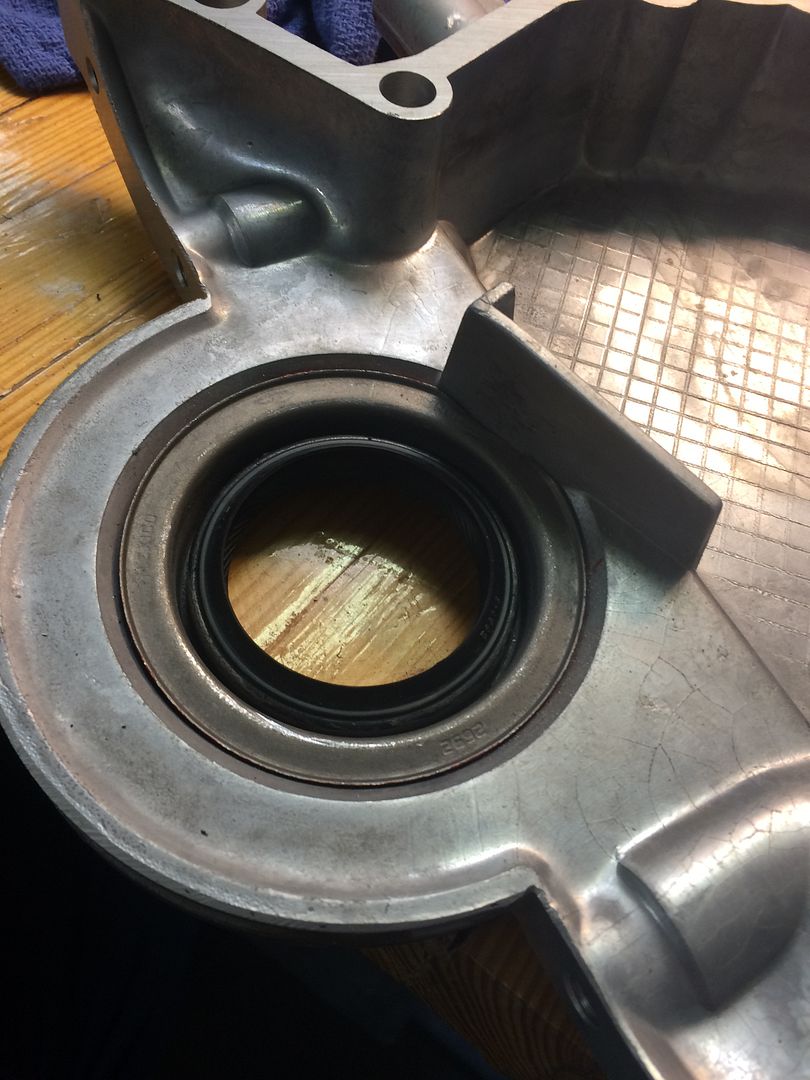
when I put the front cover on I like to put the harmonic balancer on to center the balancer in the front cover seal before I tighten the bolts on the front cover. then since most of the bolts holding the front cover on also go through the water pump I put it on as well. be sure to pull the backing plate off and add sealer on both sides of the gasket and reinstall the backing plate before putting it on the engine.
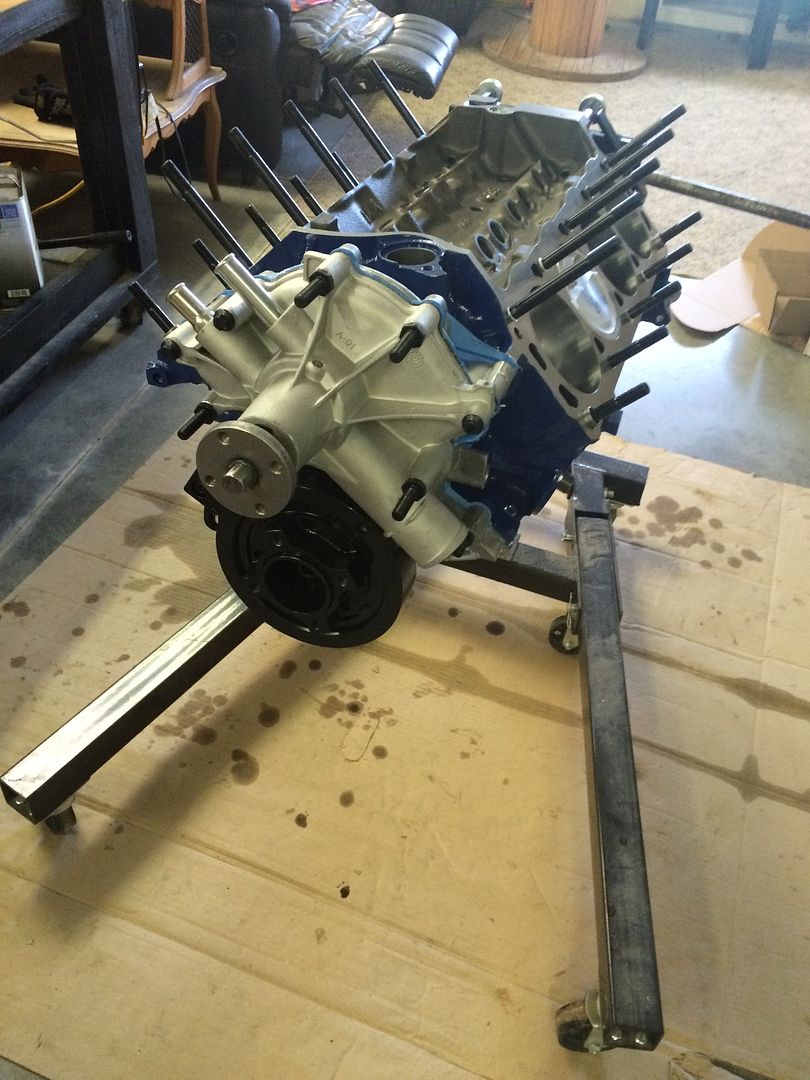
then we put the new oil pump and pickup on and checked the pickup to pan clearance with clay again before sealing up the one piece oilpan gasket on and buttoning up the bottom end.
I put a new oil filter on it and taped up the low oil sensor hole to reduce the dirt that can get in there. then I put the old heads and new intake on temporarily and wrapped it back up in plastic to await the new heads and pushrods. it will probably be 2-4 weeks before I get the new heads.